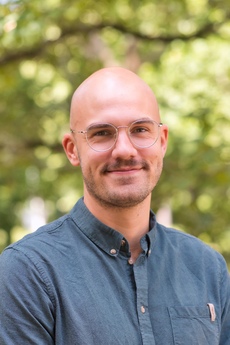
M.Sc. Felix Ellwanger
- group:
Extrusion
- room: 406
- phone: +49 721 608 48120
- fax: +49 721 608 45967
- felix ellwanger ∂does-not-exist.kit edu
Postanschrift: Kaiserstr. 12
Liefer- und Besucheranschrift: Gotthard-Franz-Straße 3
Geb. 50.31, 4. OG
D-76131 Karlsruhe
About myself
I completed both my bachelor's and master's degree in chemical engineering at the Karlsruhe Institute of Technology. My first contact with food process engineering was during my bachelor's degree course in "food technology". During my master internship at Capol GmbH in Elmshorn I was able to consolidate my interest in the food sector. There I was working in R&D on the further development of anti-sticking agents for fruit gums. During the master's course I deepened my knowledge in food process engineering and in the field of gas particle systems. In my master thesis at the Institute of Food Process Engineering I simulated the two-phase flow through an ACLR atomizer, which can be used in the field of spray drying. During my studies I enjoyed working scientifically, especially in the field of LVT, so I am looking forward to work as a research assistant at the institute of LVT.
Research focus
The extrusion process is a continuous, thermomechanical process in which various steps, such as mixing, melting and forming, take place simultaneously. In recent years, extruders have been increasingly used to produce meat analogues. For this purpose, proteins of various origins are functionalized and textured with the help of the extruder. Process conditions such as temperature, shear stress, pressure and residence time have a major influence on the reactions of the proteins. Since the process conditions always occur simultaneously during extrusion, the influence of individual process conditions on the reaction behaviour of the proteins is still unclear. In my work I therefore deal with the influence of process conditions on the reaction behaviour of proteins.
Methods
In order to further characterize the extrusion process, both experimental and numerical flow simulations are used. In the experiment, image recordings, sensors and the operating parameters of the extruder can be used to gain information about residence time distribution, temperature profiles and other important parameters. With the help of a closed cavity rheometer, it is also possible to observe individual process conditions such as the shear rate under extrusion-like conditions. This allows the pure influence of the shear rate on the reaction behavior of proteins to be investigated.
Furthermore, numerical flow simulation offers the possibility to gain insights into process variables that are not accessible in experiments. For example, the exact temperature distribution in the extruder can be determined, as well as the resulting thermal stress that affects the proteins used.